Injection - molded parts are often thin - walled structures with complex shapes. The thin - walled structure, combined with high injection speeds, results in high flow velocities and shear rates. These, along with the complex viscosity characteristics of the material, cause significant changes in the material's viscosity during mold filling.
A mold serves two main purposes in the injection - molding process:
Typically, an injection mold is a complex structure with intricate cavities and ejection systems. This complexity affects the position of cooling channels, which in turn leads to variations in mold temperature. Such variations influence the material's viscosity and its final flow characteristics.
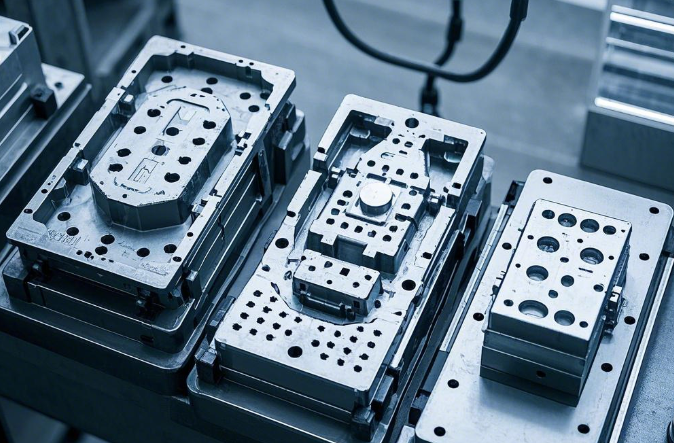
Polymer materials used for injection molding can be classified into semi - crystalline and amorphous polymers. Both types exhibit complex thermorheological behavior, which is closely related to the molding process.
Thermoplastics usually show viscoelasticity. Additionally, they have the properties of shear - thinning and pressure - induced heating. Their thermal properties change with temperature and may also be affected by the stress state. For semi - crystalline polymers, the material properties depend on the processing history and the rate of temperature change.
During the injection - molding production process, the process conditions for manufacturing qualified parts may be unstable. These instabilities are due to the inherent non - linearity of the material and the complexity of the part geometry mentioned earlier. Notably, slight deviations in process conditions can have a significant impact on product quality.
In summary, the mold - filling, pressure - holding, and cooling processes, as well as the solidification of the melt, involve several heat - transfer modes, phase changes, and time - varying boundary conditions. Moreover, material properties and part geometry further complicate this process.
To address complex injection - molding issues and ensure stable production, the injection - molding process should:
To maintain this stability, the injection stage typically uses speed control. The faster the speed, the lower the material viscosity. When the injection reaches 95% - 99%, it switches to pressure - holding, which uses pressure control.
When the injection reaches 95% - 99%, the end of the mold cavity is not fully filled with plastic, but the plastic in the mold cavity begins to cool and shrink simultaneously. That is, the V/P (velocity/pressure) switch is very unstable.
Like the two - stage molding process, it requires maintaining process stability. Additionally, the three - stage molding process has the following characteristics: The switching point is slightly advanced. After injection is completed, it enters the compensation - shrinkage stage until the cavity is filled to 99%, and then it switches to pressure - holding. The pressure - holding is only to resist the pressure in the cavity until the gate is closed.
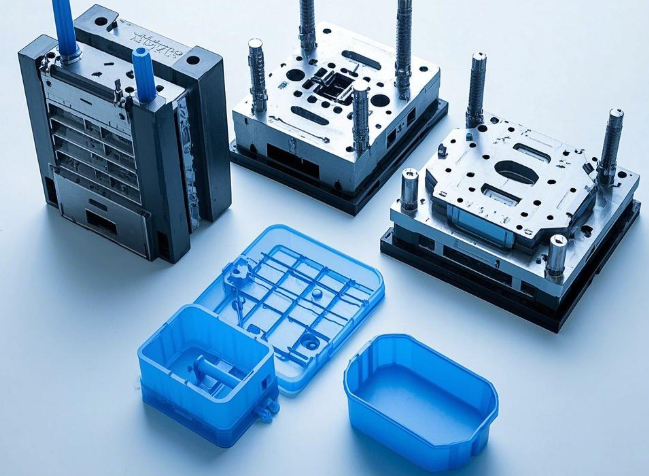
In this way, a new process sequence is formed: injection stage (speed control), compensation - shrinkage stage (speed control), and pressure - holding stage (pressure control). The compensation - shrinkage stage covers the unstable switching action, making the molding process more stable.
The advantages of the three - stage process are:
A more stable compensation - shrinkage stage for better control of plastic filling, eliminating quality problems caused by stress and over - filling.
It is more suitable for cavity pressure control.
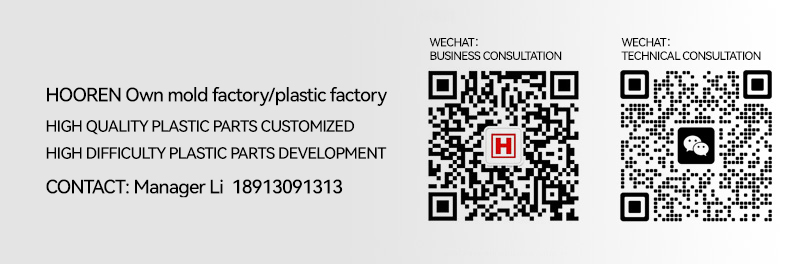