Adjusting the production process is crucial for enhancing product quality and output. Given the short injection - molding cycle, poor process control will yield numerous defective products. When making adjustments, change one condition at a time and observe carefully, as adjusting multiple factors simultaneously can cause confusion and make problem - solving difficult.
There are diverse ways to adjust the process. For example, there are over ten solutions for incomplete product filling, and the key solution must be identified. Also, note the dialectical relationships in solutions. For instance, when dealing with product depressions, sometimes raise the material temperature, sometimes lower it; sometimes increase the material amount, sometimes decrease it.
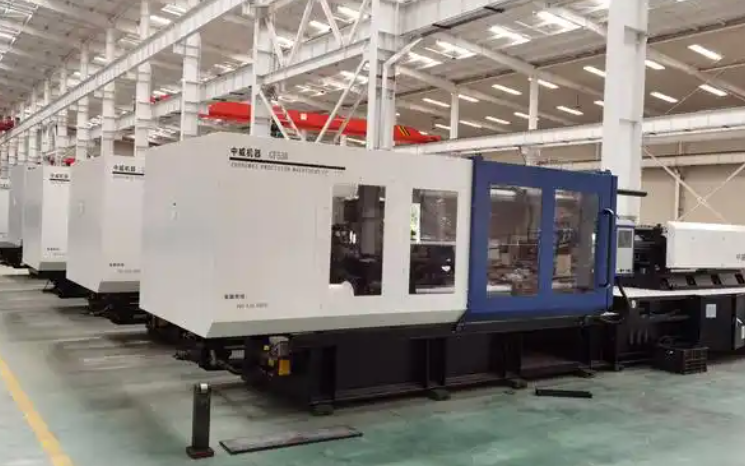
Insufficient plasticizing capacity: If the product quality approaches or exceeds the injection - molding machine's maximum injection mass, plasticization may be insufficient. Some plastics like nylon need machines with large plasticizing capacity. Replace the machine if necessary.
Inaccurate temperature indication: Malfunctions in the temperature - control device or heating coils can lead to wrong temperature readings. Check and repair or replace the faulty parts.
Improper nozzle inner - hole diameter: A too - small diameter may block the feed or consume pressure, while a too - large one reduces injection force. Also, poor nozzle - runner matching and nozzle issues can cause filling problems.
Feeding channel blockage: Plastic lumps in the feeding system, due to factors like premature melting, can block the channel. Clear the blockage to solve the problem.
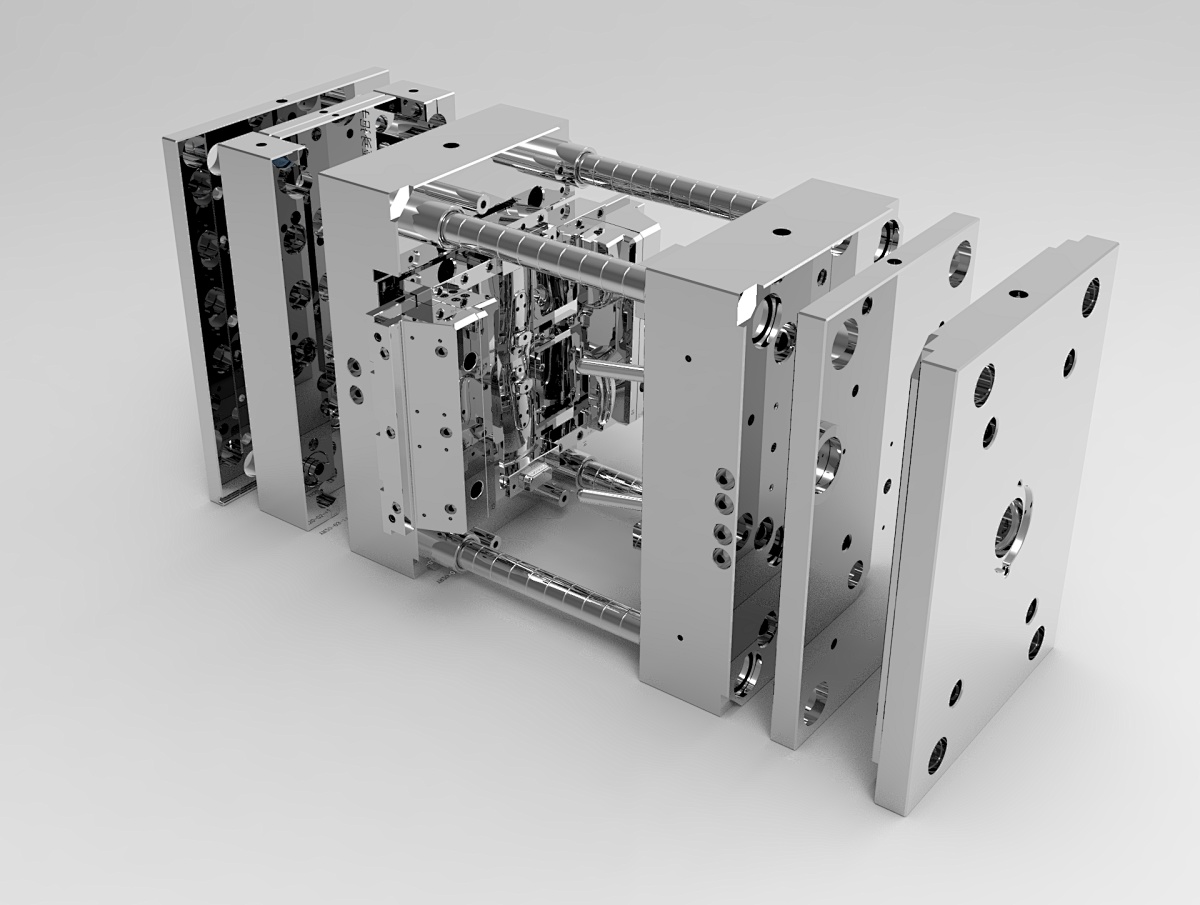
Cold material in the mold: High barrel - nozzle temperature or excessive barrel storage can cause "drooling", and cold material from the nozzle may enter the mold. Lower the temperature and reduce storage.
Short injection - molding cycle: A short cycle may not allow enough time for the material to reach the right temperature. Adjust the cycle according to the voltage, mainly focusing on the time from holding - pressure end to screw retraction.
Gating system defects: Small, rough, or wrongly - designed runners and gates can increase resistance, cause blockages, or lead to unbalanced filling. Adjust the runner and gate sizes and improve their design.
Unreasonable mold design: Complex molds with improper gates, narrow runners, or thin - walled sections may cause filling problems. Modify the mold, add vents, or adjust the number of cavities if needed.
Feeding adjustment issues: Inaccurate feeding, abnormal injection cycles, or wrong back - pressure can result in insufficient or excessive material. Adjust the feeding amount according to the material type and temperature.
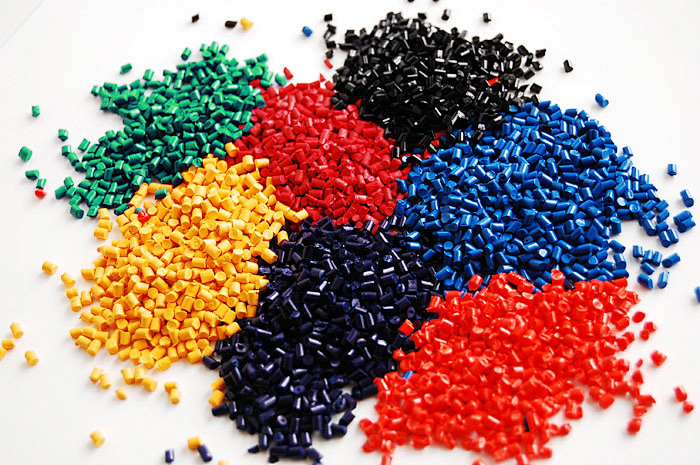
Low injection pressure and short time: High - viscosity plastics may need higher pressure and longer injection time, especially when colorants limit the barrel temperature.
Slow injection speed: For complex - shaped or high - viscosity products, high - speed injection may be required to ensure filling.
Low material temperature: Low temperatures at the barrel front, rear, or nozzle can cause filling difficulties. Adjust the temperatures and consider external heating for the nozzle if necessary.
Poor flowability: High - molecular - weight, un - dried, or improperly - formulated raw materials may have poor flowability. Dry the material, increase the barrel temperature, or change the raw - material type.
Insufficient supply: Low material in the hopper or a faulty feeding device can cause supply problems. Refill the hopper and check/repair the feeding device.
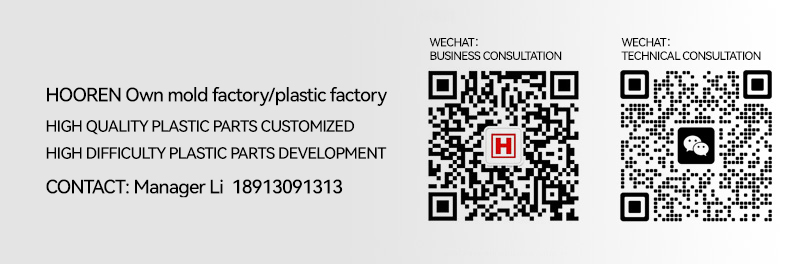