The injection molding control system is a cyclic process that contains a set of preset programs. The next cycle will run only when certain conditions are met. The inspection and monitoring of these conditions, as well as the commands for starting, ending, or continuing each cycle, are all completed by a sequence controller. The sequence controller provides "safety protection" for the injection molding machine. For example, when the front door of the injection molding machine is open, the controller does not allow the mold to move.
Set the action sequence of the injection molding machine, adjust and control the main processes and parameters of the injection molding machine.
Detect the process status and performance. Injection molding is a very typical complex nonlinear dynamic process. During molding, machine parameters, material properties, and process variables interact. The quality (dimensions, appearance, mechanical properties, etc.) of injection - molded parts cannot all be measured online. Only by controlling the key machine/process variables can the product quality and process repeatability be ensured. The relationship among equipment, materials, process variables, and product quality is as follows: (Here, it seems there is no specific content about this relationship in the original text. If there is more information, it can be added.)
High - end injection molding control systems also perform functions such as process variable management, process monitoring, and statistical analysis. How to effectively avoid interference has become an important issue in producing high - precision, complex parts with a good surface. The open - loop system (a) and the closed - loop system (b) are as follows: (Here, it seems there is no specific content about the systems in the original text. If there is more information, it can be added.)
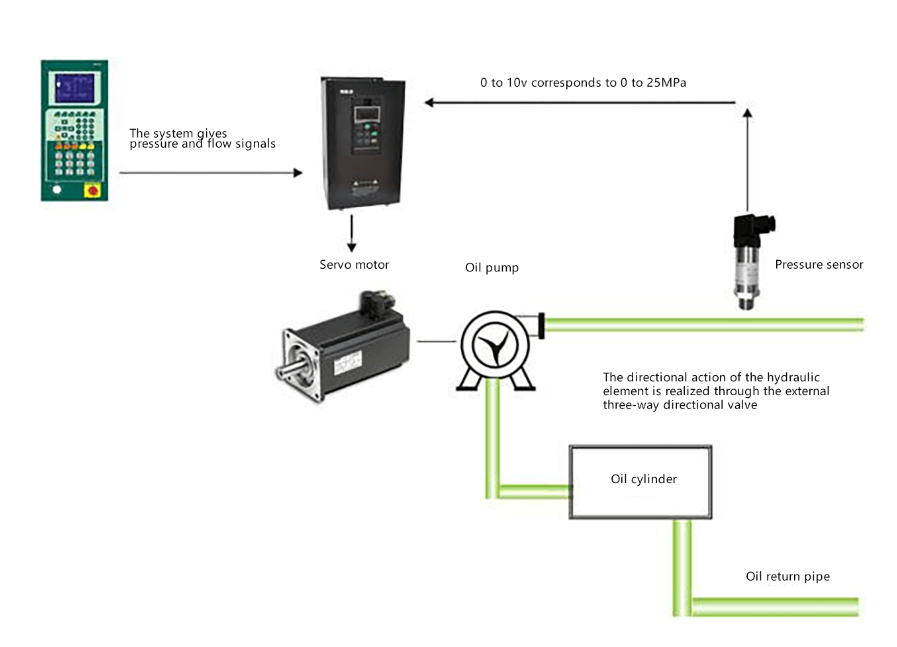
Open - loop system: An open - loop system includes equipment with a controlled variable, an actuator that drives the equipment, and a controller that sends command signals to the actuator. Taking screw speed control as an example, the control object is the screw of the injection unit, the output is the screw rotation speed, and a typical actuator is a hydraulic valve. The controller sends an opening command to the hydraulic valve at a certain speed according to the setting.
In the actual production process, there are various sources of interference. Although the open - loop system is simple and inexpensive, it cannot compensate for any interference encountered during the control process. For example, as the injection molding time progresses, the temperature of the hydraulic oil will change, which will affect the state of the hydraulic response. With the same opening of the hydraulic valve, the injection speed will change with the oil temperature. The open - loop system cannot correct the errors caused by interference.
In terms of process/injection molding machine variables, they can be divided into full - cycle and stage - specific control variables. Full - cycle controllable variables such as temperature include: melt temperature, barrel temperature, mold temperature, and hydraulic oil temperature. These are variables that need to be controlled in all cycles.
Stage - specific variables are as follows: Cavity pressure is an ideal controllable variable among stage - specific variables because it directly reflects the state of the material in the cavity. However, in actual production, a cavity pressure sensor needs to be installed in the mold, which increases the cost for some products.
Plasticizing stage: The ultimate goal is the uniformity of the melt temperature. It needs to be achieved by controlling the reasonable screw rotation speed and back pressure (a reasonable screw design may be necessary).
Filling stage: Precisely and reasonably controlling the injection speed can ensure consistent filling actions and eliminate the non - uniformity of molded parts. Short shots, sink marks, and many surface problems can be solved by adjusting the injection speed, so the injection speed is a key variable in the filling stage.
Holding pressure stage: Nozzle pressure is relatively close to the change process of cavity variables. The sensor is directly installed on the nozzle and does not need to be installed in the mold.
Mold opening - closing stage: It is necessary to achieve fast mold movement and precise mold positioning synchronously.
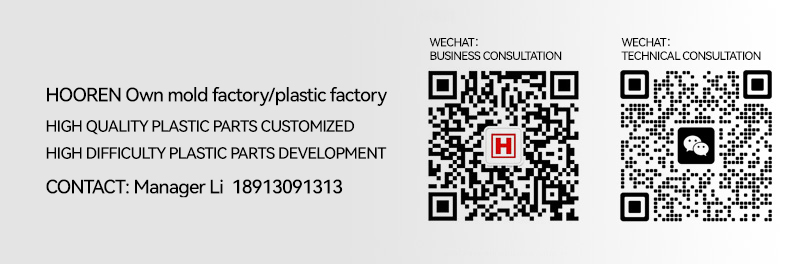