Factors affecting the quality of injection moulds
2025-02-15 09:43:02
Mold material
Product Analysis & Optimization:Prior to mould design, thoroughly analyze the product. Consider its structure, accuracy needs, appearance, and usage scenarios. For complex products, optimize the structure multiple times to ensure smooth molding and minimize defects like deformation and shrinkage.
Reasonable Mould Structure:Based on product features and production demands, design a proper mould structure. Select suitable parting surfaces, demoulding ways, and cooling systems. A good cooling system ensures uniform cooling, reduces internal stress, and improves dimensional stability.
CAE Analysis Application:Use CAE software to simulate injection molding. Predict plastic flow, temperature, and pressure in the mould. Spot potential issues like short shots, weld lines, and warpage early and optimize the mould design.
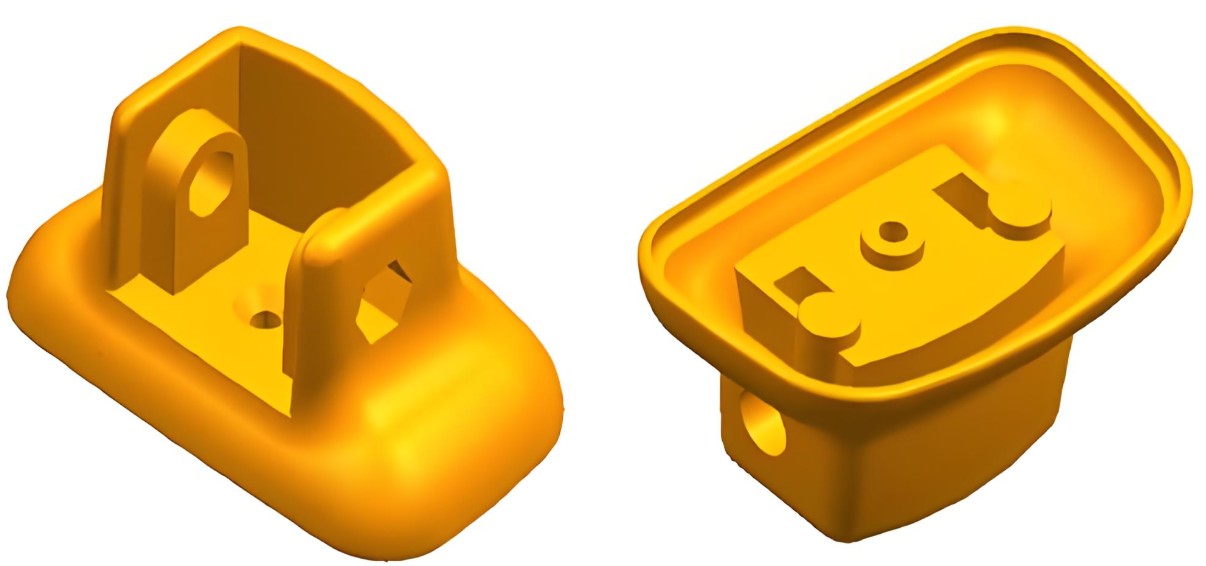
Precision Equipment & Tech:Employ advanced machining gear like high - precision CNC centers, EDM machines, etc. to ensure mould machining accuracy. Continuously upgrade machining skills and optimize parameters for better part accuracy and surface finish.
Tight Machining Accuracy Control:Strictly control the machining accuracy of all mould parts. Ensure key dimensions are within design limits using high - precision measuring tools.
Mould Assembly & Debugging:Assembly is vital for mould quality. Ensure accurate part placement and proper fit. After assembly, conduct rigorous debugging through trial - molding to identify and fix problems.
Usage - based Selection:Choose mould materials according to usage and working conditions. For high - volume, high - precision moulds, pick high - performance steels like P20 or H13 with good strength, toughness, wear, and corrosion resistance.
Quality Assurance:Source materials from reliable suppliers and demand quality certificates. Thoroughly inspect materials for chemical composition, hardness, and metallographic structure.
Parameter Tuning:Determine optimal injection pressure, speed, holding pressure, time, and cooling time through experiments and experience. Adjust parameters during production for better part quality.
Process Monitoring & Feedback:Use an advanced monitoring system to track injection parameters. Analyze data, spot anomalies, and adjust processes. Set up a quality feedback mechanism to optimize processes and moulds.
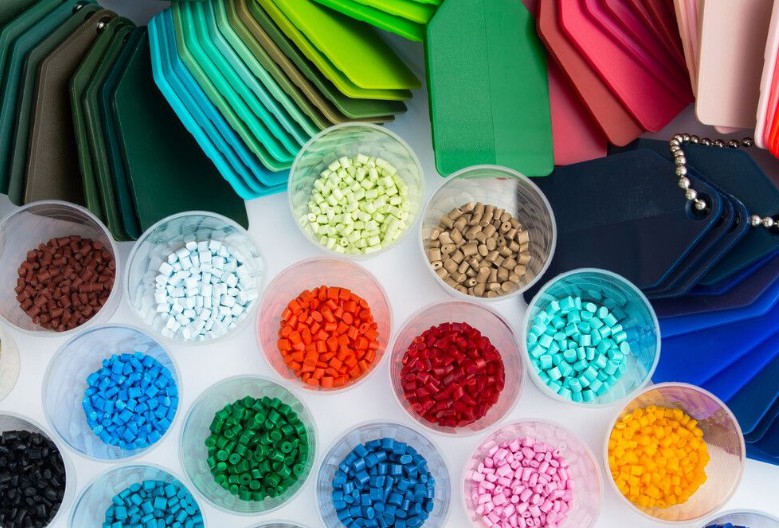
Inspection System Setup:Establish a comprehensive quality inspection system. Control quality at every stage, from design drawing review to post - trial - molding inspection.
Inspection Tools & Methods:Utilize various inspection tools like CMMs, optical projectors, etc. to check mould dimensions, surface quality, and tolerances. Verify key data multiple times.
Data Analysis & Improvement:Analyze inspection data, find quality issue roots, and take corrective actions. Continuously enhance mould quality and reliability.
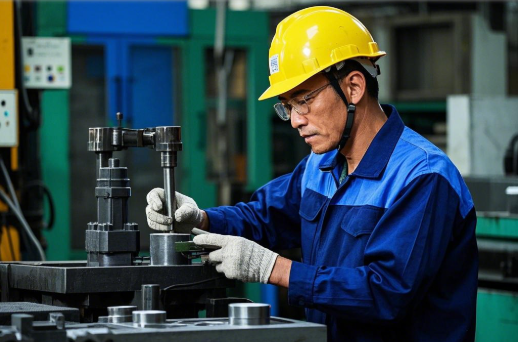
Daily Maintenance:Create a detailed maintenance plan. Regularly clean, lubricate, and tighten the mould. Keep the mould surface clean and moving parts lubricated to prevent performance degradation.
Regular Checks & Repairs:Periodically inspect the mould for wear, deformation, and cracks. Replace or repair issues promptly. Stock spare parts for quick replacement.
Rust Prevention & Storage:Apply rust - prevention treatment when the mould is not in use. Store it in a dry, well - ventilated area.
Skill Training:Train mould - related staff on design, manufacturing, and debugging. Organize internal training and invite experts to keep employees updated on the latest technologies.
Quality Awareness Cultivation:Instill quality management awareness in all employees. Ensure they follow quality procedures and work details to maintain mould quality.
Teamwork & Communication:Since mould production involves multiple departments, foster teamwork and communication. Set up a communication mechanism to enable smooth information flow and problem - solving.
Improving injection mould quality is a systematic task. Address design, manufacturing, materials, processes, inspection, maintenance, and personnel aspects. Control each link tightly to produce high - quality moulds for plastic production.
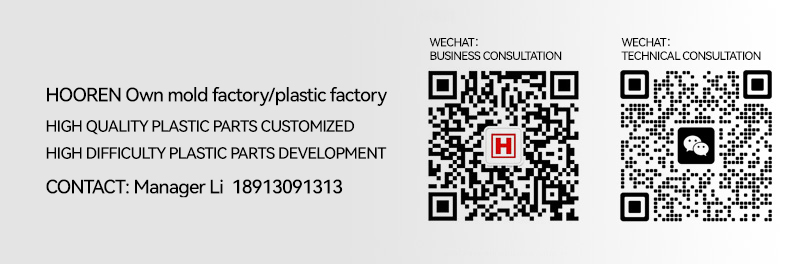