Precautions and solutions for burnt injection molding products
2025-02-11 09:05:39
Injection molding products
Burnt injection - molded products are a common and challenging issue in injection molding, which affects the appearance, performance, and lifespan of products. The following elaborates from four aspects and provides cases, causes, and solutions:
Reasonable Exhaust System Design
During injection molding, if the gases in the mold cavity cannot be discharged in time, they will be compressed and heat up, causing local burning of plastics. For example, the narrow exhaust grooves in a mobile phone case mold led to edge burning. The solution is to design exhaust grooves according to product and material characteristics, with a depth of 0.02 - 0.05mm and a width of 1.5 - 3mm. Add exhaust holes in prone - to - burn areas or use breathable steel.
Regular Mold Cleaning
Oil stains, impurities, and release agent residues on the mold surface can impede plastic flow and cause burning, as seen in automotive interior parts. Regularly clean the mold thoroughly with special cleaners and equipment, dry it, and apply rust - inhibitor. Also, conduct a simple cleaning before production.
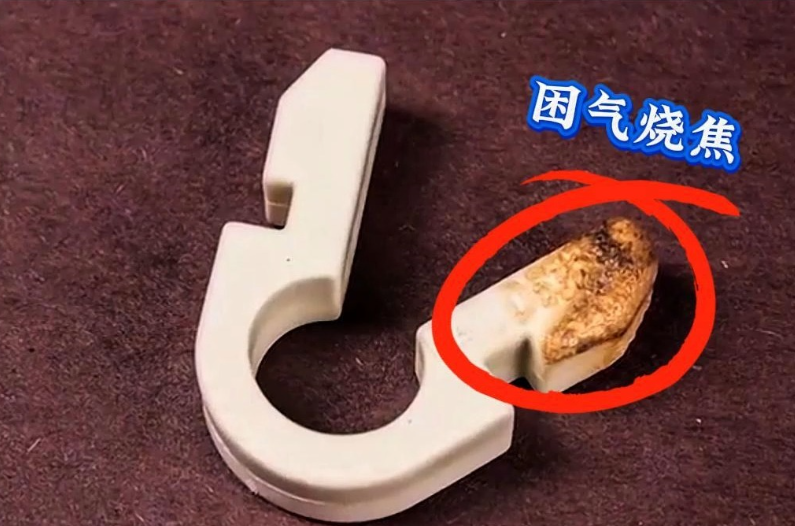
Control of Injection Speed
Too - fast injection speed generates high shear heat, leading to burning, like in the case of a thin - walled plastic cup. Adjust the injection speed based on product and material properties: 60 - 80mm/s for thin - walled products and 30 - 50mm/s for thick - walled products, and find the optimal value gradually.
Optimization of Holding Pressure and Time
Excessive holding pressure or time can cause burning, as in plastic gears. Determine appropriate holding pressure (30% - 60% of injection pressure) and time (5 - 10s) through experiments, adjusting pressure first and then time.
Selection of Suitable Plastic Materials
Some plastics are prone to burning at high temperatures. For example, ordinary PP burns when over 230℃, while modified PP can avoid this. Select materials according to product requirements, considering thermal stability, fluidity, etc.
Sufficient Drying of Plastic Raw Materials
Moisture in raw materials can cause burning, as in PET plastic bottles. Dry materials according to their characteristics, such as drying PA at 80 - 120℃ for 4 - 6 hours and PET at 120 - 160℃ for 6 - 8 hours, and check moisture content regularly.
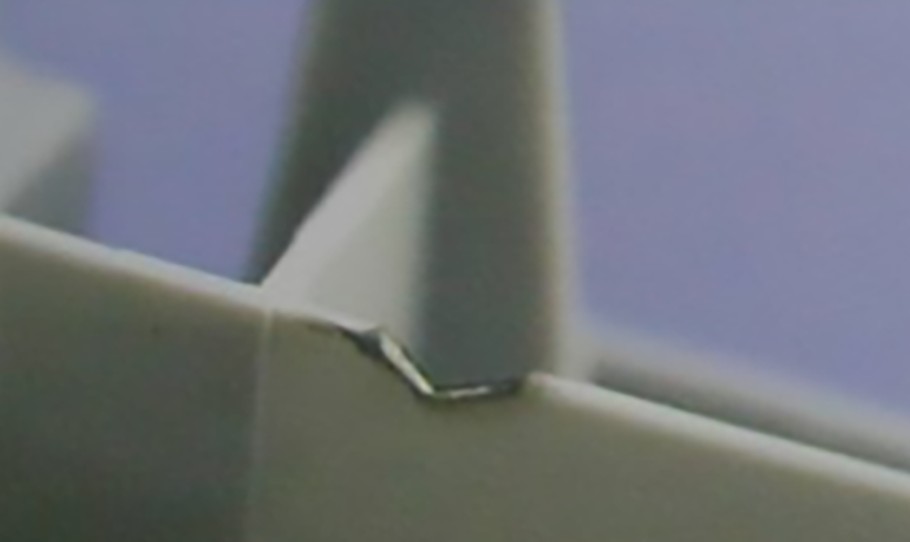
Inspection of the Heating System
Malfunctions in the heating system can cause barrel temperature issues and plastic burning, as in plastic pipe production. Regularly check heating coils, calibrate temperature sensors monthly, and update controllers. Stop production immediately for repairs when problems are detected.
Cleaning of the Screw and Barrel
Accumulations in the screw and barrel can carbonize and cause new materials to burn, as in plastic toy production. Regularly disassemble and clean them, polish the inner walls, check for wear, and clean thoroughly when changing materials or colors.
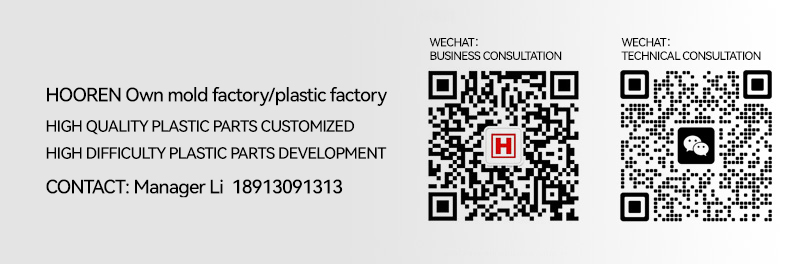