The full name of "melt index" is "melt flow index", which is one of the commonly used indicators in the plastic processing field. There are hundreds of different types of PP resin alone, and the melt index has become an important basis for people to select grades.
Melt Flow Index (MI)
It refers to the weight value of the melt of thermoplastic plastics passing through a standard capillary within ten minutes under a certain temperature and pressure, expressed in (g/10min). The larger the MI value, the lower the viscosity and average molecular weight of the raw material, the better the processing performance, and the better the fluidity. Conversely, the smaller the MI value, the larger the viscosity and average molecular weight of the raw material, the worse the processing performance, and the worse the fluidity, but the higher the physical and mechanical properties.
For the raw materials of the same grade, multiple processing and usage will lead to a decrease in their molecular weight, thus increasing the melt flow rate and deteriorating the physical and mechanical properties of the products. This is also the main reason why recycled plastics have a large melt flow rate.
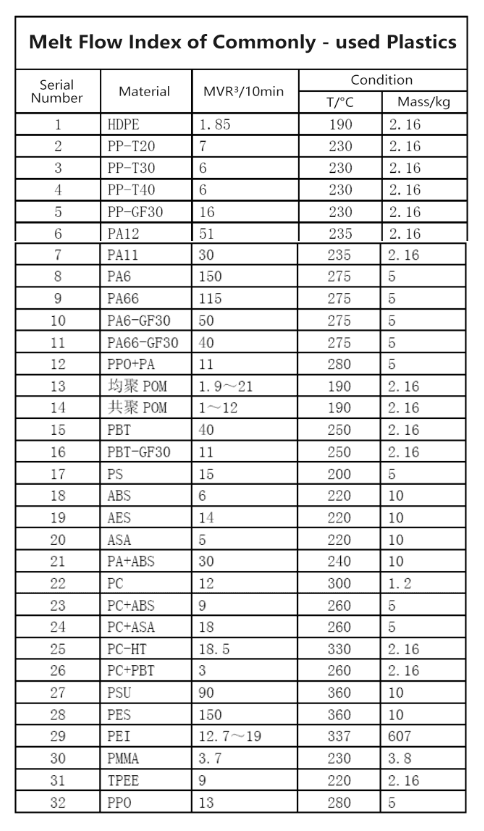
Testing Principle
Under a certain temperature and load, the amount of thermoplastic plastics flowing through a standard capillary within a specified time reflects the flow performance of the plastics in the molten state. Usually, under the specified temperature and load conditions, the plastic particles are heated to the molten state, and then a specific instrument is used to measure the mass flowing out from the capillary within the specified time.
Methods of Adjusting the Melt Index
Blending with grades of different melt indexes in the same category can change the melt index of the raw material to a certain extent.
Adding crosslinking agents, such as some organic peroxides, with an addition amount of about one-thousandth. This method has a relatively large impact on the mechanical properties.
Adding a small amount of fillers, such as submicron calcium carbonate, can reduce the melt index and appropriately improve the mechanical properties.
There is an additive called a melt index modifier, also known as a polymer binder. It is a kind of processing modifier for polyolefin products developed according to the normal molecular structure mechanism of polyolefin products. Through various bonding technologies, polyolefin polymers are effectively aggregated, thus increasing the attractive force (i.e., van der Waals force) between polymer chain segments. Through this modification process, the performance of the partially degraded polyolefin products can be restored to the performance before chain scission, and the single performance can also be greatly improved according to different addition amounts.
Influencing Factors
The melt index is a parameter characterizing the flow rate of the raw material in the screw. It measures the fluidity of the polymer under a given shear force and is related to the shear force and temperature.
Materials with a high melt index have a relatively small friction coefficient with the screw in the extruder, so the output is relatively small. Generally, materials with a high melt index have more impurities, exert greater pressure on the machine head, and are likely to cause screen blockage.
Temperature: When the temperature rises, the movement ability of the molecular chain increases, the viscosity of the plastic decreases, and the melt index increases. Conversely, when the temperature decreases, the melt index decreases. Different plastics have different sensitivity to temperature. For example, polyethylene is relatively more sensitive to temperature changes.
Pressure: Increasing the pressure can accelerate the flow rate of the plastic melt in the capillary, resulting in an increase in the melt index. Generally, within a certain range, there is a positive correlation between the pressure and the melt index.
Molecular Weight: The larger the molecular weight, the longer the molecular chain, the stronger the intermolecular force, the higher the melt viscosity of the plastic, and the smaller the melt index. Conversely, the smaller the molecular weight, the larger the melt index.
Molecular Structure: Structural factors such as the degree of branching and crystallinity of the molecular chain will also affect the melt index. Plastics with a high degree of branching have relatively fewer entanglements between molecular chains, better fluidity, and a higher melt index. For plastics with high crystallinity, due to the existence of the crystalline region restricting the movement of the molecular chain, the melt index is usually lower.
Importance and Applications
Selection of Plastic Processing Technology: In the injection molding process, if the melt index of the plastic is too low, it may lead to difficulties in mold filling, such as defects like lack of material and short shot. While if the melt index is too high, it may cause problems such as flash and overflow. Therefore, according to the melt index of the plastic, appropriate injection molding process parameters can be selected, such as injection temperature, injection pressure, and holding pressure time.
Quality Control of Plastic Materials: The melt index is one of the important indicators for the quality control of plastic raw materials. For different batches of plastic raw materials, if there is a large fluctuation in the melt index, it may mean that the molecular weight distribution and molecular structure of the materials have changed, which will affect their processing performance and the quality of the final products.
Research and Development of New Products: When developing new plastic materials or improving existing materials, the melt index is an important reference indicator. By adjusting the formulation and production process of the materials and controlling the melt index within an appropriate range, plastic materials with good processing performance and physical properties can be obtained.
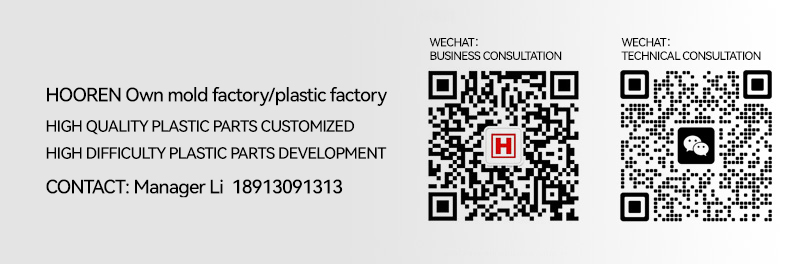