SA, a hard and transparent material, resists internal stress cracking well. It has high transparency, with a softening temperature and impact strength higher than PS. Styrene in SA makes it hard, transparent, and easy to process, while acrylonitrile provides chemical and thermal stability. SA can bear loads, resist chemical reactions, thermal deformation, and maintain geometric stability. Adding glass fiber boosts its strength, thermal deformation resistance, and reduces thermal expansion. SA's Vicat softening temp is around 110 °C, deflection temp under load about 100 °C, and shrinkage rate 0.3 - 0.7%.
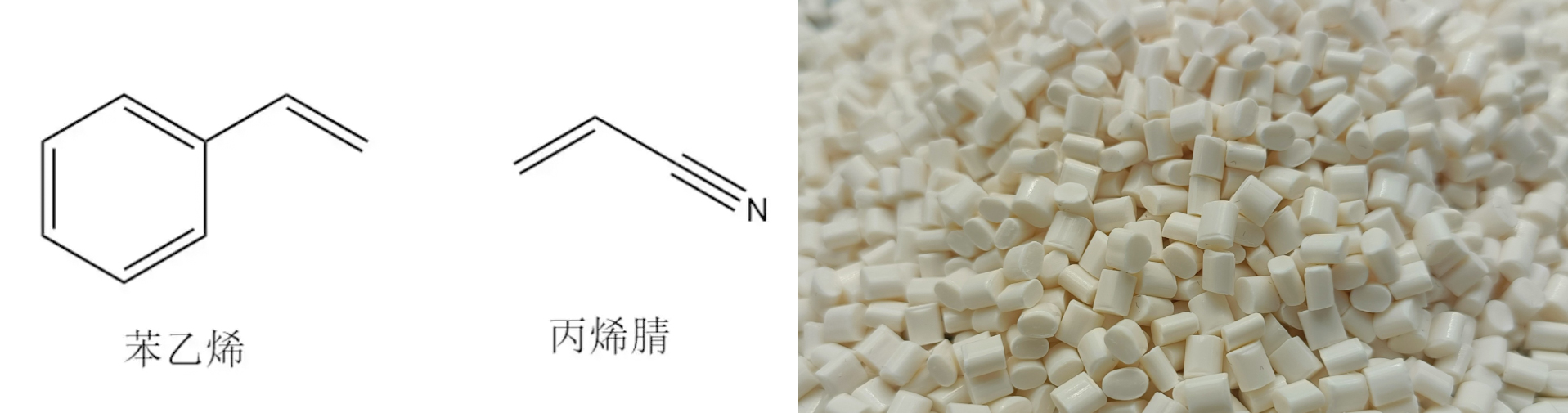
SA is processed at 200 - 250 °C. Being hygroscopic, it must be dried over an hour before use. Its fluidity is a bit worse than PS, so injection pressure (350 - 1300 bar) should be slightly higher, and high - speed injection is advised. The mold temp is set at 45 - 75 °C. If not stored right, SA absorbs moisture. Recommended drying is at 80 °C for 2 - 4 hours, with a melting temp of 200 - 270 °C. For thick - walled items, use a lower melting temp. For reinforced SA, mold temp should not exceed 60 °C. A well - designed cooling system is crucial as mold temp impacts product appearance, shrinkage, and bending. All regular gates work, but the size must be proper to avoid stripes, burns, and voids.
Electrical (sockets, housings)
Daily goods (kitchenware, fridge parts, TV bases)
Automotive (headlight boxes, mirrors, dashboards)
Household (tableware, food knives)
Cosmetic packaging (safety glass, water filter housings)
Medical (syringes, dialysis gear)
Packaging (cosmetic boxes, bottle caps)
Special items (lighter housings, fishing gear, toothbrush handles)
Drying: SA, being hygroscopic, needs drying before molding. Moisture causes surface defects. Dry at 70 - 80 °C for 2 - 4 hours to reduce water content below 0.1%.
Coloring: Add masterbatches (1% - 5% depending on color depth) for specific colors and mix well.
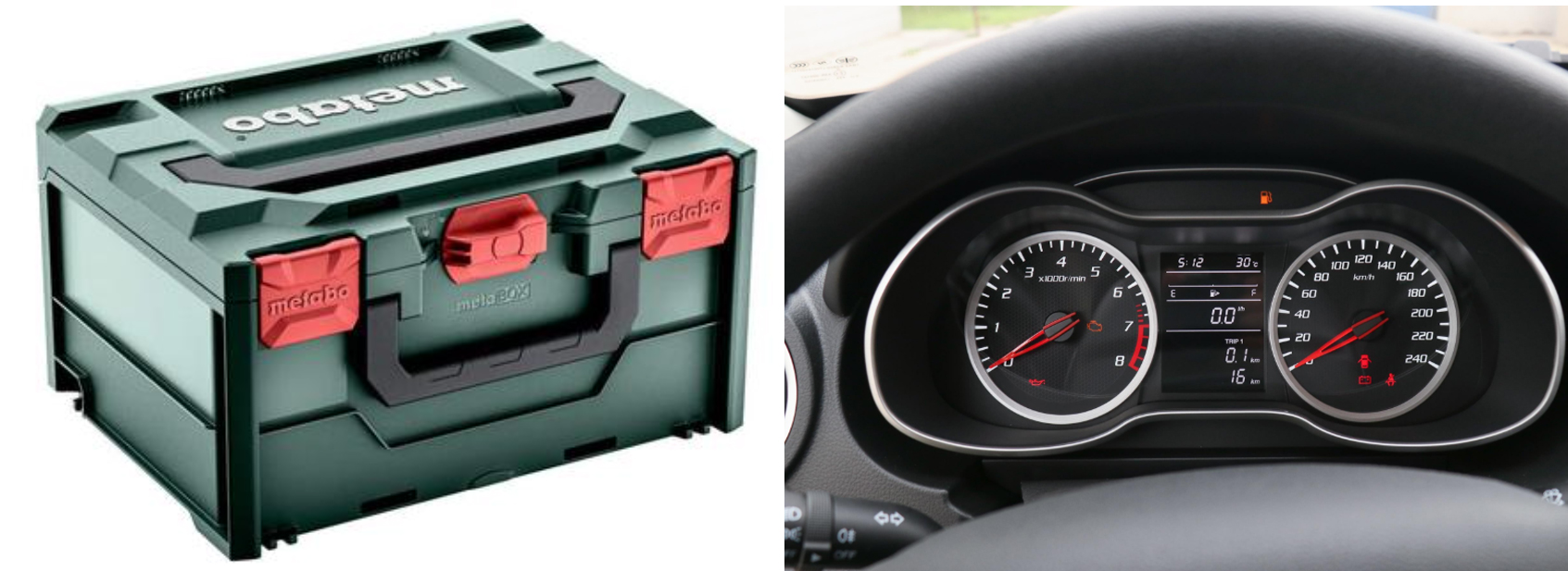
Selection: Pick a screw - type machine with an L/D ratio of 18 - 22. Clamping force is 1 - 3 tons per cm2 of product projected area.
Temp Control: Barrel temp: 180 - 200 °C (hopper end), 200 - 220 °C (middle), 220 - 240 °C (nozzle end); nozzle at 220 - 230 °C. Mold temp is 60 - 80 °C.
Injection pressure is 70 - 120 MPa. Injection speed, 30 - 80 mm/s, is adjusted by product thickness: higher for thin - walled, lower for thick - walled.
Close the moving and fixed molds at a moderate speed to prevent overflow and damage.
Inject plasticized SA into the mold, watching for pressure and speed changes.
Apply 50% - 70% of injection pressure as holding pressure for 3 - 5 seconds per mm of product thickness.
Cool the product in the mold for 10 - 30 seconds, depending on thickness.
Open the mold and eject the product. Use release agents and choose the right demolding method.
Trim flash with tools or machines.
Do surface treatments like polishing, painting, or electroplating.
Check product quality by inspecting appearance, dimensions, and performance.
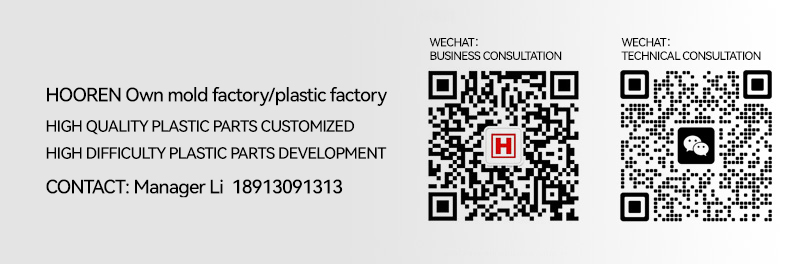